What is Aluminium Extrusion?
Aluminium extrusion is a process in which aluminium alloy is forced through a die to create a desired shape or profile. The process involves heating the aluminium to a malleable state, and then pressing it through a mold using a powerful hydraulic press. The resulting profile can be customized to fit specific requirements, making it an ideal solution for a wide range of applications.
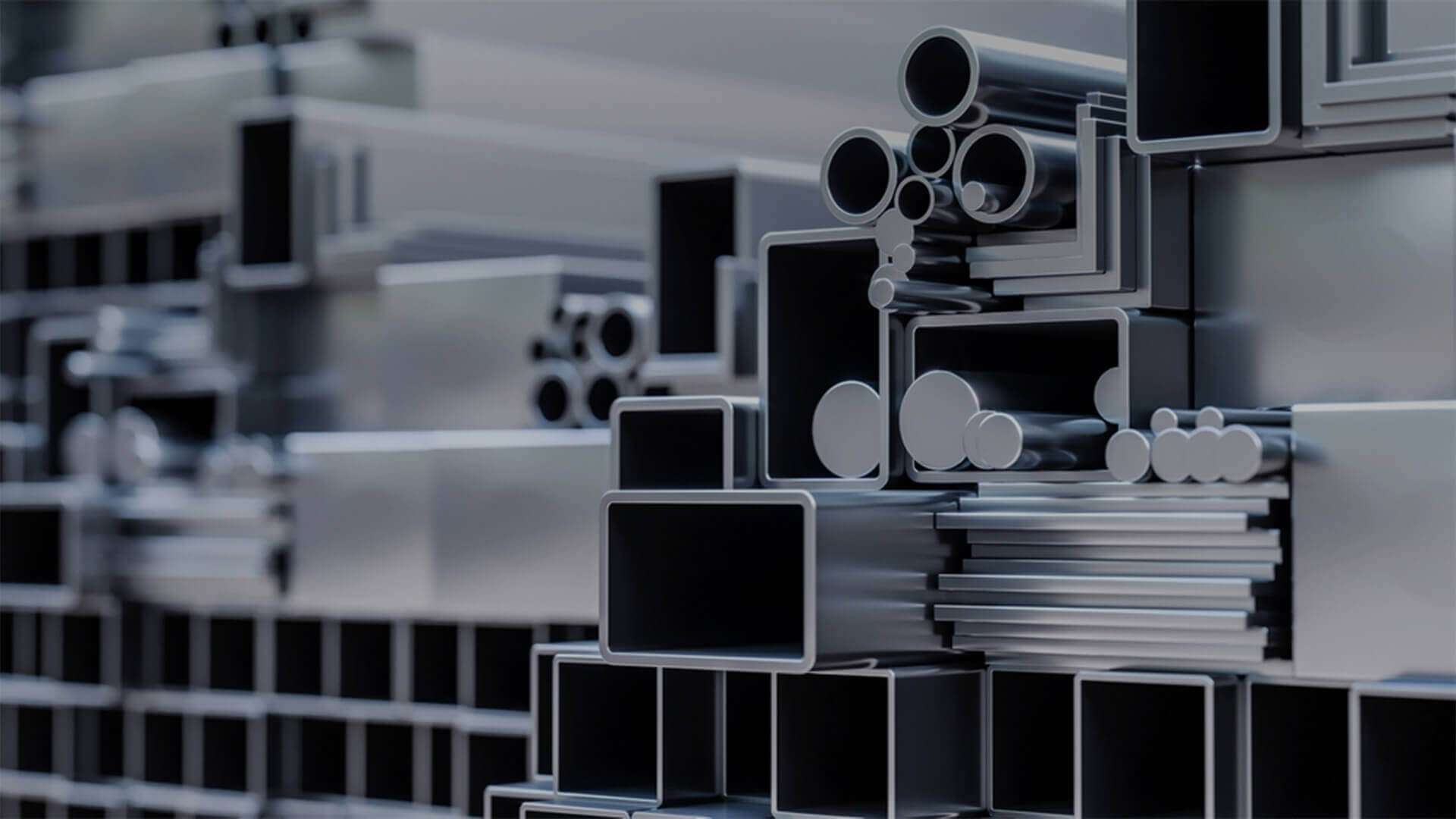
In the world of manufacturing, aluminium extrusion has become a vital process that has revolutionized the way we produce goods. From aircraft parts to automotive components, aluminium extrusion has proven to be a versatile and efficient method for creating lightweight, strong, and durable products. In this article, we will explore the ins and outs of aluminium extrusion and how it has become a game-changer in various industries.
Advantages of Aluminium Extrusion
One of the primary benefits of aluminium extrusion is its ability to create complex shapes and profiles with ease. Unlike other manufacturing processes, extrusion allows for the creation of long, continuous lengths of extruded aluminium, making it an efficient and cost-effective option. Additionally, aluminium extrusion offers several other advantages, including:
- Lightweight: Aluminium is a lightweight material, making it an ideal choice for industries where weight is a critical factor, such as aerospace and automotive.
- Strength: Aluminium extrusions are incredibly strong, with a high strength-to-weight ratio that makes them suitable for a variety of applications.
- Corrosion-resistant: Aluminium is naturally corrosion-resistant, which means that extruded profiles can withstand harsh environments without degrading.
- Customizable: Aluminium extrusions can be tailored to fit specific requirements, including shape, size, and surface finish.
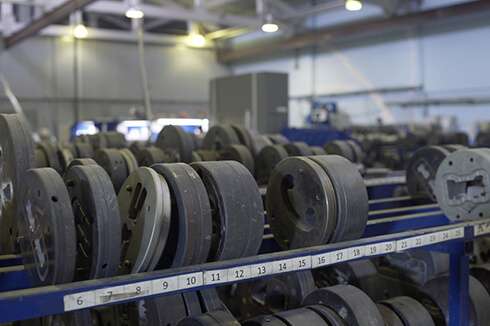
Industries That Benefit from Aluminium Extrusion
Aluminium extrusion has become an integral part of various industries, including:
- Automotive: Aluminium extrusions are used in the automotive industry for lightweight, high-strength components such as engine blocks, cylinder heads, and transmission parts. Using aluminium extrusions helps improve fuel efficiency, reduce emissions, and increase the overall performance of vehicles.
- Aerospace: Aluminium extrusions are widely used in the aerospace industry for lightweight, high-strength components such as aircraft structures, engine mounts, and landing gear. Using aluminium extrusions helps reduce fuel consumption and increase the overall efficiency of aircraft.
- Construction: Aluminium extrusions are used in the construction industry for lightweight, high-strength components such as window frames, door frames, and roofing systems. The use of aluminium extrusions helps to reduce the overall weight of buildings, which can lead to cost savings on foundation and structural materials.
- Electrical: Aluminium extrusions are used in the electrical industry for components such as heat sinks, bus bars, and cable management systems. The use of aluminium extrusions helps to improve the efficiency of electrical systems, reduce heat buildup, and increase the overall reliability of electrical components.
- Medical: Aluminium extrusions are used in the medical industry for lightweight, high-strength components such as medical equipment frames, surgical instruments, and prosthetic devices. The use of aluminium extrusions helps to improve the mobility and durability of medical equipment, and can also reduce the overall weight of prosthetic devices for improved patient comfort.
- Consumer Goods: Aluminium extrusions are used in the consumer goods industry for products such as bicycle frames, luggage frames, and outdoor furniture. The use of aluminium extrusions helps to improve the durability, strength, and lightweight properties of these products, making them more functional and convenient for consumers.
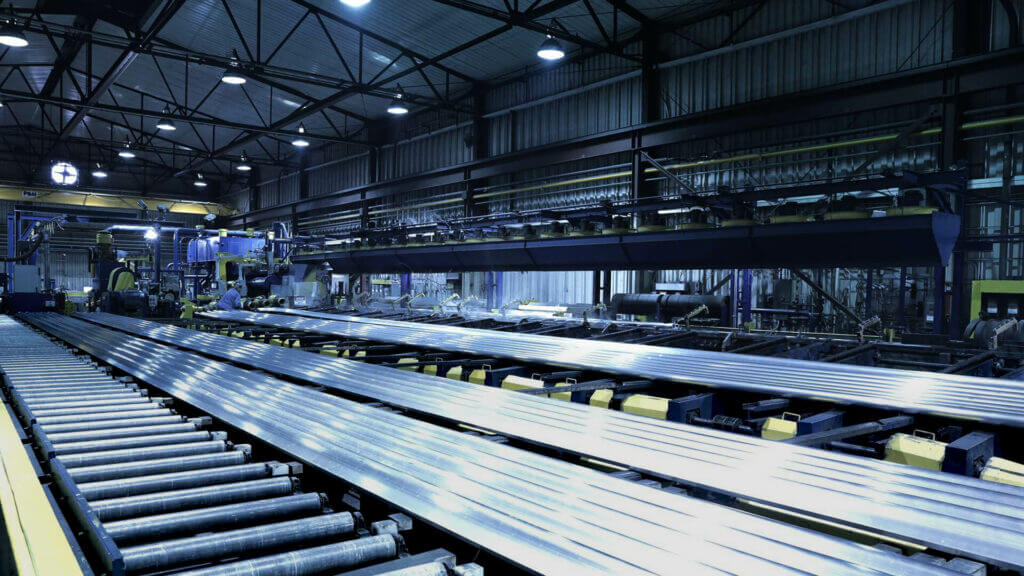
The Future of Aluminium Extrusion
As technology continues to advance, the possibilities for aluminium extrusion are endless. With the rise of 3D printing and robotics, the manufacturing process is becoming more streamlined and efficient. At SNALCO, we are committed to staying at the forefront of innovation, pushing the boundaries of what is possible with aluminium extrusion.